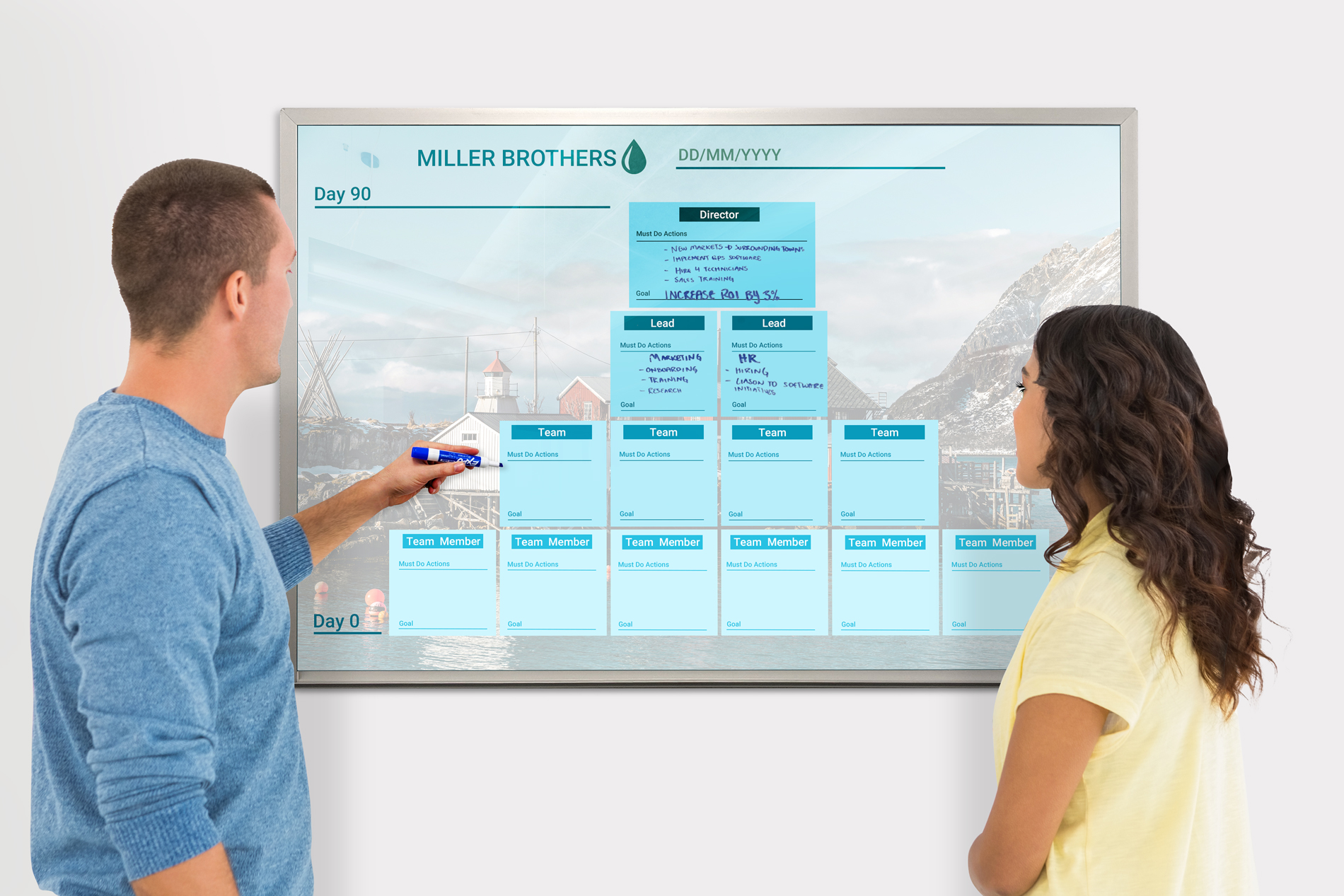
MyWhiteBoards has been the number one choice of manufacturers for crafting heavy-duty dry erase products that can handle a rugged factory setting. Lean manufacturing dry erase boards eliminate waste and help streamline operations in companies to ensure maximum productivity.
What is Lean Manufacturing?
Lean manufacturing is a manufacturing methodology with the primary purpose of addressing the single biggest killer of productivity: waste. Lean focuses on minimizing waste from manufacturing systems while maximizing productivity.
Lean manufacturing has profoundly influenced the manufacturing world and expanded its influence outside the manufacturing world in the past 31 years since its advent. The book The Machine That Changed the World by James P Womack, Daniel T. Jones, and Daniel Roos of MIT discusses the introduction of the lean methodology in the Toyota Production System, which revolutionized the company's manufacturing process.
A lean production system focuses on reducing waste, creating customer value, and seeking continuous process improvement. Reducing waste can be achieved by applying lean project management principles, techniques, and tools.
The lean methodology has become so popular that it has spread into healthcare, software development, and service industries. Introducing lean methodology to your enterprise can bolster success and ramp up productivity.
What is Waste? What is Value?
The key to optimizing lean is understanding customers' value of their products and services. From the customer's perspective, waste can be defined as an activity that does not add value to a product or service. Value is created by the producer but determined by the customer. This leads companies to understand the price of their products as what customers are willing to pay. Any industry has a great deal of waste, whether it be through idle workers or unused material that cannot be repurposed or recycled. All lead to the same result of a drag on productivity.
The Five Principles of Manufacturing
Lean manufacturing has many different principles that make up its mentality and process. Knowing these principles allows you to curate the perfect lean layout for your business. Let's dive into the principles of lean!
Identify Value from Customer Perspective
Identifying value from the customer perspective comes from understanding what the customers believe is valuable in the product. Understanding what a customer thinks is a fair price for the labor and product production is the key to understanding the value you aim to create.
Map the Value Stream
Companies must study each cycle stage intently, identifying and eliminating anything that does not add value. This can be achieved by recording and analyzing information flow, product production, or service. This principle is combing through your production line from start to finish and identifying where waste occurs.
Create Flow
The creation of flow is critical to eliminating waste and optimizing the process. Lean manufacturing prevents interruptions and works to create a consistent stream of activities in the process.
Establish a Pull System
Lean manufacturing is designed to use a pull system instead of a push system to eliminate waste. A push system typically determines the inventory needed in advance, meaning the product is manufactured to meet the expected orders. Lean enables the pull system, in which nothing is brought or made until there is a demand. When demand for a specific product is needed, the product is created, resulting in less waste and less money being spent.
Pursue Perfection with Continual Process Improvement
Lean manufacturing embodies the mentality of continuously striving for the perfection of no waste. This comes from consistently targeting the root cause of waste and eliminating it from the value stream. Continual process improvement ensures that you always strive to find the best production process throughout innovation and change.
How Dry Erase Aids in Lean Manufacturing
Physical displays like whiteboards in high-traffic areas are proven to increase success because they act as visual reminders, which are 20% more effective than oral reminders. Visual aids like Lean Whiteboards, shown below, ensure that no gaps, interruptions, or wasteful actions stand out. We offer many lean whiteboard designs from 5S to Poka-Yoke and Kanban. Let's take a look at some of our boards.
The Gantt Chart
The Gantt Chart visualizes a timeline of overlapping tasks when a project or product is launched. Gantt charts are perfect for tasks with a tight timeline from start to finish and help with the overall goal of decreasing the time between production. This time between productions is considered "waste" in the lean manufacturing mentality, and Gantt aims to eliminate waste while maximizing the short production timeline.
Get your Gantt Whiteboard Here!
The Fishbone Diagram aka the Root Cause
A Fishbone Diagram is a manufacturing tool that breaks down production problems to the root cause. The fishbone aims to answer the question "why?" It's a tool in lean when implementing organizational structural changes. These changes can be anything from floor layout changes or anything that will impact day-to-day operations. The board displayed above shows the visuals of the Plan, Do, Check, Act that provides a basis for continuous improvement. Having a space meant for action items not only holds your team accountable but also decreases decision-making fatigue.
Let's Design your Fishbone Board Here.
Classic Kanban Board
Kanban is one of the most common project management visuals in lean because it has a simple design. The design is focused on the production and highlights any potential issues before they arise in manufacturing. The Kanban board is used to identify bottlenecks that need immediate attention before they cause significant issues and waste. Teams that use a physical Kanban board achieve a steadier workflow and fewer interruptions.
Get your Company Kanban Board Here.
The Value Added Stream Map
In a market economy, the organization with the best efficiency and effectiveness will come out on top. The Value Added Stream Map is a popular manufacturing board as it provides a "big picture" view of the entire supply chain and helps a production manager trace problems back to the root problem. Value Added Stream Maps can help your production team implement "Just in Time Manufacturing" by tracking batches in the supply chain. Data can be taken from the daily rundown and added to a KPI table, enabling information transparency across any time frame.
Design your Value Added Stream Map Here.
Measuring success is a critical part of embracing lean methodology. Production and operation managers invest in “Lean Boards” to display many other critical success factors like Lead Time, Production Volume, Right First Time, Equipment Effectiveness, Days Since Last Accident, Defect Density, and more. It all depends on your organizational goals.
Gallery of Lean Boards
Why Choose OptiMA?
We are a small business making our products in the USA. We specialize in dry erase boards, dry erase wallcoverings, portable dry erase units, high-quality custom printed whiteboards, fast shipping, and five-star customer service. Over the last three decades, we've worked hard to deliver industrial-quality whiteboard solutions that won't break customers' budgets.
If you have an idea for a custom whiteboard, call us at 866-366-1500 or head to our website to learn more about our products!
Sources:
- Daniel, D. (2020, April 15). What is lean Manufacturing? SearchERP. ReManufacturing15, 2022, from https://www.techtarget.com
- What are lean Manufacturing and the 5 principles used? TWI. (n.d.). Retrieved July 15, 2022, from https://www.twi-global.com
- Lean production. Introduction to Lean Manufacturing | Lean Production. (n.d.). Retrieved July 15, 2022, from https://www.leanproduction.com/